AI-powered defect detection systems: Use cases, role in quality control, development considerations and future trends
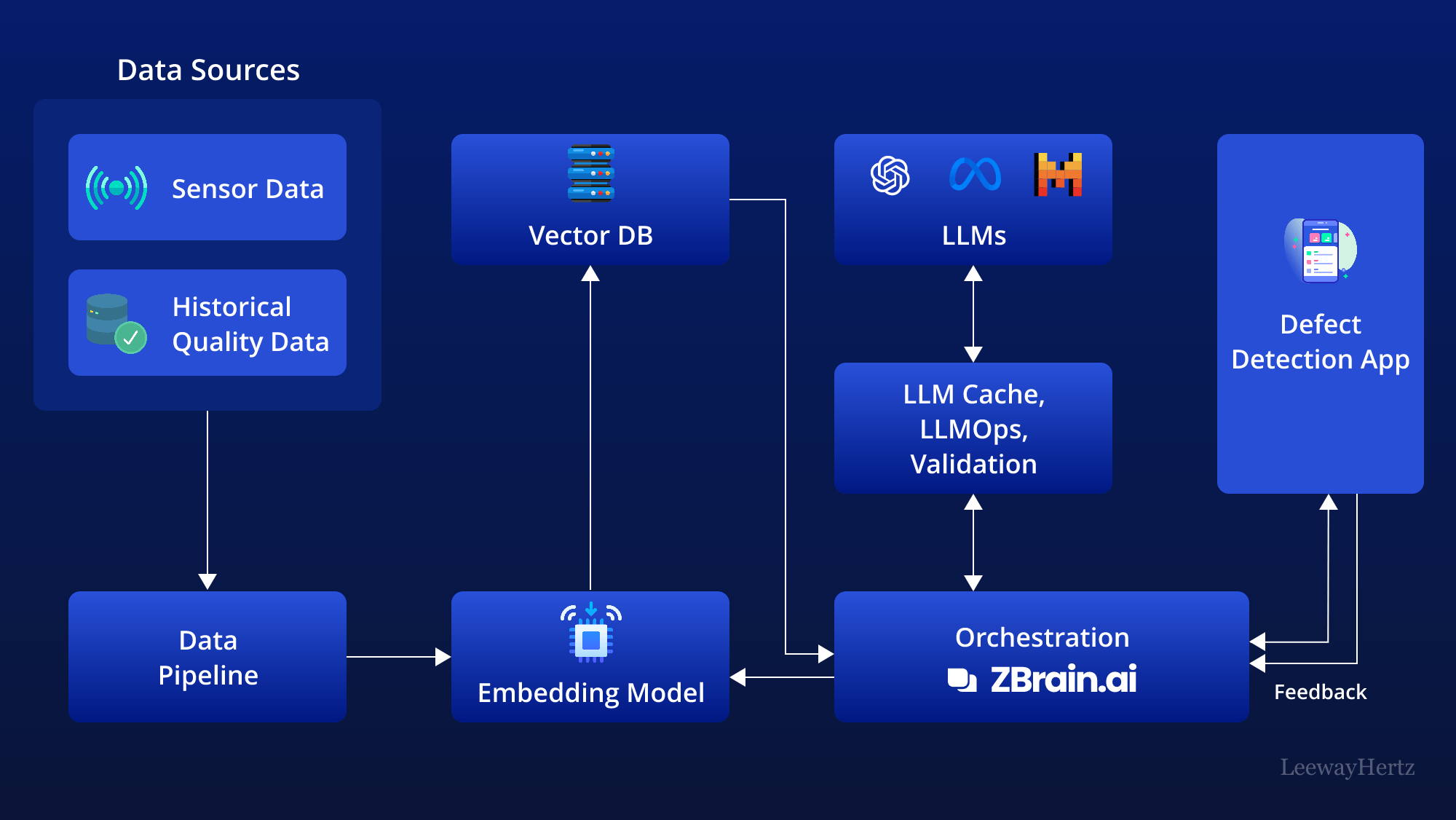
In today’s fast-paced manufacturing landscape, ensuring product quality is paramount for businesses to maintain their competitive edge and meet customer expectations. One of the critical aspects of quality control is defect detection, where even the slightest imperfection can lead to significant consequences in terms of product performance, customer satisfaction, and brand reputation. Traditional defect detection methods, while effective to a certain extent, often fall short in detecting subtle defects or adapting to evolving production processes. However, with the advent of AI and ML technologies, a new era of defect detection has emerged, promising more accurate, efficient, and adaptable solutions. AI-powered defect detection systems leverage advanced computational techniques to analyze large volumes of data and identify patterns indicative of defects, offering several advantages over traditional methods.
This article delves into the intricacies of building effective AI-powered defect detection systems for quality control. It covers the entire process, from problem definition and data collection to model development, deployment, and maintenance. Specifically, the article explores the technical aspects of data preprocessing, feature extraction, model selection, and evaluation. Additionally, it discusses the considerations, challenges, and best practices involved in building AI-powered defect detection systems. Through detailed explanations and practical insights, readers will gain a comprehensive understanding of how to harness AI and ML technologies to enhance defect detection capabilities and improve overall product quality.
- What is a defect detection system?
- Role of defect detection systems in quality control processes
- Overview of AI-powered defect detection systems
- Traditional defect detection systems vs AI-powered defect detection systems
- How does an AI-powered defect detection system for quality control work?
- Build an AI-powered defect detection system for quality control
- Considerations for building AI-powered defect detection systems
- How can LeewayHertz help in building AI-powered defect detection systems?
- LeewayHertz’s AI development services for defect detection systems
- Industries and domains benefiting from building AI-powered defect detection systems
- Future trends and innovations in AI-powered defect detection systems
What is a defect detection system?
A defect detection system is a technological solution designed to identify and categorize defects or abnormalities in products, materials, or processes. These systems play a crucial role in quality control across various industries, ensuring that manufactured goods meet specific standards of quality and reliability.
These systems utilize various methods and technologies to detect defects, ranging from traditional manual inspections to sophisticated automated processes powered by artificial intelligence and machine learning algorithms.
Here are the key components and functionalities of a defect detection system:
- Sensing technology: Defect detection systems often employ advanced sensing technologies to capture data about the product or process under inspection. Depending on the nature of the defects being detected, these may include visual sensors, cameras, lasers, ultrasonic sensors, X-ray systems, or infrared sensors.
- Data acquisition: Once the sensing technology captures data, it is processed and digitized for analysis. This step involves converting analog signals into digital format for further processing.
- Image processing and analysis: For visual defect detection systems, image processing techniques are applied to analyze captured images or videos. This involves preprocessing steps such as noise reduction, image enhancement, and segmentation to isolate regions of interest.
- Feature extraction: Relevant features are extracted from the processed data to characterize potential defects. These features may include shape, color, texture, size, and intensity variations, depending on the type of defects being targeted.
- Defect classification: Based on the extracted features, machine learning algorithms or rule-based systems classify detected anomalies into different categories of defects. Classification algorithms learn patterns from labeled training data to distinguish between defective and non-defective items.
- Decision-making: Defect detection systems make decisions based on the classification results. Depending on the application, decisions may involve rejecting defective products, triggering alarms, initiating corrective actions, or providing feedback for process optimization.
- Integration with control systems: In industrial settings, defect detection systems are often integrated with control systems to enable real-time monitoring and control of manufacturing processes. This integration facilitates immediate corrective actions to minimize the production of defective items.
- Continuous improvement: Defect detection systems typically incorporate mechanisms for continuous improvement and adaptation. This may involve feedback loops where performance metrics are monitored, and the system is recalibrated or retrained periodically to maintain optimal performance.
Defect detection systems find applications across various industries, including manufacturing, automotive, electronics, pharmaceuticals, food processing, and aerospace. These systems contribute to improving product quality, reducing waste, enhancing operational efficiency, and ensuring compliance with regulatory standards.
Role of defect detection systems in quality control processes
The role of defect detection systems in quality control processes is paramount, as they serve as the frontline defense against substandard products, ensuring that only items meeting predefined quality standards are released to the market. Here’s a detailed exploration of their role:
- Early detection of defects: Defect detection systems enable the early identification of defects in products or materials during various stages of the manufacturing process. By detecting defects promptly, they prevent the production of further defective items, minimizing waste and reducing associated costs.
- Maintaining product quality: Quality control is essential to maintain the reputation of a brand and ensure customer satisfaction. Defect detection systems play a critical role in upholding product quality by identifying and removing defective items before they reach consumers. This helps in preserving brand integrity and loyalty.
- Reducing manufacturing costs: Detecting defects early in the production process can significantly reduce manufacturing costs associated with rework, scrap, and warranty claims. By eliminating defective items early on, defect detection systems help manufacturers optimize their production processes and improve overall efficiency.
- Ensuring compliance with standards and regulations: Many industries are subject to stringent quality standards and regulatory requirements. Defect detection systems help manufacturers ensure compliance with these standards by systematically identifying and addressing deviations from established quality criteria.
- Enhancing process optimization: Defect detection systems provide valuable data and insights into the root causes of defects, enabling manufacturers to identify process inefficiencies and areas for improvement. By analyzing defect patterns and trends, manufacturers can optimize their production processes to prevent future occurrences of defects.
- Real-time monitoring and control: In modern manufacturing environments, defect detection systems are often integrated with real-time monitoring and control systems. This integration allows manufacturers to continuously monitor production processes and take immediate corrective actions when deviations or defects are detected, ensuring consistent product quality.
- Facilitating continuous improvement: Defect detection systems contribute to a culture of continuous improvement within organizations by providing feedback on product quality and process performance. By analyzing historical defect data and performance metrics, manufacturers can identify opportunities for optimization and implement corrective actions to prevent defects in the future.
- Supporting supply chain management: Quality defects can have ripple effects throughout the supply chain, impacting suppliers, distributors, and ultimately end customers. Defect detection systems help manufacturers identify and address quality issues early in the production process, minimizing disruptions to the supply chain and ensuring on-time delivery of high-quality products.
Defect detection systems play a critical role in quality control processes by enabling early detection of defects, maintaining product quality, reducing manufacturing costs, ensuring compliance with standards and regulations, enhancing process optimization, facilitating real-time monitoring and control, supporting continuous improvement, and optimizing supply chain management. They are indispensable tools for manufacturers striving to deliver high-quality products and maintain a competitive edge in today’s marketplace.
Overview of AI-powered defect detection systems
AI-powered defect detection systems utilize artificial intelligence (AI) and machine learning (ML) algorithms to automatically identify and categorize defects or anomalies in products, materials, or processes. These systems leverage advanced computational techniques to analyze large volumes of data and detect patterns indicative of defects, offering several advantages over traditional defect detection methods. These systems are capable of processing various types of data, including images, sensor readings, and process parameters, allowing for comprehensive defect detection across diverse manufacturing environments. By continuously learning from labeled training data, AI-powered defect detection systems can adapt to evolving production conditions and new types of defects, ensuring robust performance over time. Integration with automation systems enables seamless implementation of closed-loop control, where detected defects trigger immediate corrective actions, minimizing the production of defective items. Overall, AI-powered defect detection systems represent an advanced solution for improving product quality, reducing manufacturing costs, and enhancing overall efficiency in industrial settings.
Traditional defect detection systems vs AI-powered defect detection systems
Here’s a comparison of traditional defect detection systems and AI-powered defect detection systems presented in a tabular format:
Aspect | Traditional defect detection systems | AI-powered defect detection systems |
---|---|---|
Technology used | Relies on manual inspection by human operators or rule-based systems. | Utilizes artificial intelligence (AI) and machine learning (ML) algorithms for automated defect detection. |
Data processing | Limited ability to process large volumes of data efficiently. | Capable of analyzing large datasets in real-time, enabling quick detection of defects. |
Flexibility | May lack flexibility and adaptability to new types of defects. | Highly adaptable to different types of defects and production environments, can be retrained to recognize new patterns. |
Scalability | Limited scalability, may require additional resources for scaling up. | Highly scalable, can handle increasing volumes of data and production throughput with ease. |
Accuracy | Subject to human error and variability. | Offers high accuracy and consistency in defect detection, reduces false positives and false negatives. |
Training requirements | Limited training required for human operators, may require specific expertise for rule-based systems. | Requires initial training on labeled datasets, ongoing monitoring and retraining for optimal performance. |
Real-time processing | Limited capability for real-time processing. | Capable of processing data in real-time, enabling immediate detection and response to defects. |
Integration with automation systems | Integration may be challenging due to reliance on manual inspection. | Seamlessly integrates with automation systems, enables closed-loop control for automatic defect detection. |
Cost | Initial setup costs may be lower, but ongoing labor costs can be significant. | Initial investment may be higher due to technology adoption, but long-term savings from reduced labor costs and improved efficiency. |
Continuous improvement | Limited ability to learn and improve over time. | Supports continuous learning and improvement through feedback loops and enhances performance over time. |
Optimize Your Operations With AI Agents
Optimize your workflows with ZBrain AI agents that automate tasks and empower smarter, data-driven decisions.
This table provides a concise comparison of traditional defect detection systems and AI-powered defect detection systems, highlighting their differences in terms of technology used, data processing capabilities, flexibility, scalability, accuracy, training requirements, real-time processing, integration with automation systems, cost, and continuous improvement.
How does an AI-powered defect detection system for quality control work?
AI enhances defect detection in quality control processes by automating inspection tasks, improving detection accuracy, and speeding up the production cycle. Incorporating AI into a defect detection system leverages advanced Large Language Models (LLMs) and connects them with vast data repositories. This approach significantly enhances the ability to identify, analyze, and rectify production flaws.
The structured architecture of the AI-powered defect detection system integrates these components:
- Data sources: Effective defect detection relies on a variety of precise data inputs, including:
- High-resolution imaging: Images captured through high-definition cameras during production to visually inspect products for defects.
- Sensor data: Readings from sensors integrated into production equipment, providing real-time data on operational conditions that may affect product quality.
- Historical quality data: Archives of past inspection results and identified defects, aiding in pattern recognition and predictive analysis.
- Manufacturing parameters: Specific details about production settings, such as temperature, speed, and pressure, which influence the final product quality.
- Supplier quality records: These records document the quality and consistency of materials provided by suppliers. This data allows manufacturers to correlate the quality of incoming materials with the occurrence of product defects.
- Data pipelines: The data from these varied sources are routed through data pipelines that manage their ingestion, cleaning, and structuring, making the data ready for deeper analysis.
- Embedding model: An embeddi ng model processes this structured data, converting it into numerical representations called vectors, suitable for analysis by AI systems. Major AI developers like OpenAI, Google, and Cohere provide embedding models.
- Vector database: The vectors generated by the embedding model are stored in a vector database such as Pinecone, Weaviate, or PGvector, enabling efficient and rapid querying.
- APIs and plugins: APIs and plugins like Serp, Zapier, and Wolfram play a key role by connecting different components and enabling additional functionalities, such as accessing extra data, integrating with third-party tools or performing specific tasks with ease.
- Orchestration layer: The orchestrating layer is critical in managing the workflow. ZBrain is an example of this layer that simplifies prompt chaining, manages interactions with external APIs by determining when API calls are required, retrieves contextual data from vector databases, and maintains memory across multiple LLM calls. Ultimately, this layer generates a prompt or series of prompts that are submitted to a language model for processing. The role of this layer is to orchestrate the flow of data and tasks, ensuring seamless coordination across all the components of the defect detection system.
- Query execution: The data retrieval and generation process begins when the user submits a query to the defect detection app. Queries related to specific defect types or quality concerns are submitted to the defect detection system.
- LLM processing: Once received, the app transmits the query to the orchestration layer. This layer retrieves relevant data from the vector database and LLM cache and sends it to the appropriate LLM for processing. The choice of LLM depends on the nature of the query.
- Output: The LLM generates an output based on the query and the data it receives. It can identify and categorize defects, providing detailed reports on the nature and location of quality issues.
- Defect detection app: This specialized application presents the AI-detected defects in a user-friendly format, allowing quality control engineers to take swift corrective action.
- Feedback loop: User feedback on the LLM’s output is another important aspect of this architecture. The system incorporates user feedback to continuously improve the accuracy and relevance of the AI’s outputs.
- Agent: AI agents step into this process to address complex problems, interact with the external environment, and enhance learning through post-deployment experiences. They achieve this by employing advanced reasoning/planning, strategic tool utilization, and leveraging memory, recursion, and self-reflection.
- LLM cache: Tools like Redis, SQLite, or GPTCache are used to cache frequently accessed information, accelerating the AI system’s response time.
- Logging/LLMOps: Throughout this process, LLM operations (LLMOps) tools like Weights & Biases, MLflow, Helicone and Prompt Layer help log actions and monitor performance. This ensures the LLMs operate at peak efficiency and evolve consistently through ongoing feedback mechanisms.
- Validation: A validation layer is employed to validate the LLM’s output. This is achieved through tools like Guardrails, Guidance, Rebuff, and LMQL to ensure the accuracy and reliability of the information provided.
- LLM APIs and hosting: LLM APIs and hosting platforms are essential for executing defect detection and quality control tasks and hosting the application. Depending on the requirements, developers can select from LLM APIs offered by companies such as OpenAI and Anthropic or opt for open-source models. Similarly, they can choose hosting platforms from cloud providers like AWS, GCP, Azure, and Coreweave or opt for opinionated clouds like Databricks, Mosaic, and Anyscale. The choice of LLM APIs and cloud hosting platforms depends on the project’s needs and preferences.
This structured solution architecture outlines how AI enhances defect detection in quality control, leveraging sophisticated data analysis and automated processes to improve product quality and operational efficiency.
How to build an AI-powered defect detection system for quality control?
Building an AI-powered defect detection system for quality control involves several steps, ranging from data collection and preprocessing to model development and deployment. Here’s a detailed step-by-step guide covering the technical aspects of building such a system:
Problem definition and domain understanding
In the initial phase of building an AI-powered defect detection system, it is crucial to define the specific problem that the system will address and to gain a deep understanding of the domain in which it operates. This involves clearly defining the scope of the defect detection task, such as identifying defects in manufactured products or materials. Additionally, consulting domain experts is essential to gather insights into the types of defects that need to be detected, as well as understanding the characteristics of these defects, the intricacies of production processes, and the applicable quality standards. By defining the problem and understanding the domain thoroughly, the development team can ensure that the defect detection system is tailored to meet the specific needs and challenges of the industry, resulting in a more effective and accurate solution.
Data collection and annotation
During the data collection and annotation phase of building an AI-powered defect detection system, the focus is on gathering the necessary data and preparing it for model training. This involves collecting a diverse and representative dataset that includes examples of both defective and non-defective items. Depending on the nature of the defects and the application domain, the data can be sourced from various sources, such as images, sensor readings, or other relevant data types.
Once the data is collected, it needs to be annotated to label instances of defects and non-defective items. Annotation is the process of marking or tagging each data sample with its corresponding label, indicating whether it contains a defect or not. This labeling allows the machine learning algorithms to learn the patterns associated with defects and distinguish between defective and non-defective items during training.
Annotation can be performed manually by human annotators, who carefully inspect each data sample and assign the appropriate label based on predefined criteria. Alternatively, automated annotation methods using rule-based algorithms or heuristics can be employed to label the data automatically, especially for large datasets where manual annotation may be impractical.
Overall, the data collection and annotation phase is crucial for providing the training data necessary to develop accurate and robust defect detection models, laying the foundation for the subsequent stages of model training and evaluation.
Data preprocessing
Data preprocessing is a critical step in building an AI-powered defect detection system as it involves preparing the collected data for training the model. This phase typically consists of several tasks aimed at cleaning, transforming, and organizing the data to improve the performance and reliability of the defect detection model.
Firstly, preprocessing involves tasks such as resizing images, normalizing pixel values, or removing noise from sensor data. Resizing images ensures that all input images are of the same size, which is necessary for consistency in model training. Normalizing pixel values involves scaling the pixel values to a standard range, such as [0, 1] or [-1, 1], to facilitate convergence during training. Removing noise from sensor data helps to enhance the signal-to-noise ratio, ensuring that the model can focus on relevant features and patterns.
Additionally, data preprocessing involves splitting the dataset into training, validation, and test sets. The training set is used to train the defect detection model, while the validation set is used to tune hyperparameters and evaluate the model’s performance during training. The test set, which is separate from the training and validation sets, is used to assess the final performance of the trained model on unseen data, providing an unbiased estimate of its generalization ability.
Overall, data preprocessing plays a crucial role in preparing the collected data for training the defect detection model, ensuring that it is clean, consistent, and well-organized. By performing tasks such as resizing images, normalizing pixel values, removing noise, and splitting the dataset, data preprocessing lays the groundwork for the subsequent stages of model development and evaluation.
Feature extraction and engineering
Feature extraction and engineering are crucial steps in building an AI-powered defect detection system. They involve transforming raw data into a format suitable for training a machine learning model. This phase focuses on extracting relevant features from the preprocessed data to effectively characterize potential defects.
Firstly, feature extraction involves identifying and extracting relevant information from the preprocessed data that can help discriminate between defective and non-defective items. For example, in image-based defect detection, features such as texture, color, shape, and intensity gradients may be extracted using image-processing techniques. Similarly, in signal-based defect detection, features such as frequency components, amplitude, and temporal patterns may be extracted using signal processing methods.
Furthermore, feature engineering may involve augmenting the dataset to enhance the discriminative power of the features. Data augmentation techniques such as rotation, translation, flipping, or adding noise to images can artificially increase the diversity of the training data, leading to better generalization and robustness of the defect detection model.
Additionally, if the feature space is high-dimensional or contains redundant information, dimensionality reduction techniques such as principal component analysis (PCA) or t-distributed stochastic neighbor embedding (t-SNE) may be applied to reduce the complexity of the data and improve model efficiency and performance. Dimensionality reduction helps retain the most informative features while discarding irrelevant or redundant ones, thereby improving the model’s ability to capture underlying patterns and detect defects accurately.
Overall, feature extraction and engineering play a critical role in building an effective defect detection system by transforming raw data into meaningful features that capture the characteristics of defects. By leveraging techniques such as image processing, signal processing, data augmentation, and dimensionality reduction, this phase enhances the discriminative power of the features and improves the performance of the defect detection model.
Model selection and development
Model selection and development is a critical phase in building an AI-powered defect detection system. It involves selecting an appropriate machine learning or deep learning model architecture and training the selected model using annotated training data. This phase focuses on developing a model that can effectively detect defects in the given dataset.
Firstly, model selection involves choosing a suitable machine learning or deep learning architecture that is well-suited for defect detection tasks. In many cases, convolutional neural networks (CNNs) are commonly used for image-based defect detection tasks due to their ability to learn hierarchical representations of features from image data automatically. CNNs are particularly effective at capturing spatial dependencies and patterns within images, making them well-suited for identifying defects in visual data.
Once a suitable model architecture is selected, the next step is to train the model using the annotated training data. During the training process, the model learns to distinguish between defective and non-defective items by adjusting its parameters based on the provided training examples. The training data is passed through the model iteratively, and the model’s parameters are updated using optimization algorithms such as stochastic gradient descent (SGD) or Adam to minimize the prediction error.
Furthermore, fine-tuning the model’s parameters is essential to optimize its performance on the validation set. This involves adjusting hyperparameters such as learning rate, batch size, and regularization parameters to achieve the best possible performance. Hyperparameter tuning is typically done through a process of experimentation and validation, where different combinations of hyperparameters are evaluated on the validation set, and the best-performing model is selected based on the validation performance.
Overall, model selection and development are critical steps in building an effective defect detection system. By choosing an appropriate model architecture and training the model using annotated data, developers can create a model that accurately detects defects in the given dataset, laying the foundation for subsequent phases such as evaluation, deployment, and maintenance.
Model evaluation and validation
Model evaluation and validation are crucial steps in building an AI-powered defect detection system. They involve assessing the trained model’s performance and identifying areas for improvement. This phase ensures that the developed model meets the desired quality standards and performs effectively in detecting defects.
Firstly, model evaluation involves assessing the performance of the trained model on a separate test set that was not used during the training or validation phases. This test set provides an unbiased estimate of the model’s generalization ability and its ability to detect defects in unseen data. The model’s performance is evaluated using appropriate evaluation metrics such as accuracy, precision, recall, and F1 score, which provide insights into its ability to classify defective and non-defective items correctly.
Furthermore, conducting error analysis is essential to identify common failure modes and areas for improvement in the model’s performance. This involves analyzing the misclassified instances and understanding the reasons behind the model’s errors. Common failure modes may include false positives (incorrectly identifying non-defective items as defective) or false negatives (incorrectly classifying defective items as non-defective). By conducting error analysis, developers can gain insights into the limitations of the model and identify potential areas for refinement.
Additionally, iterating on the model development process is crucial to address any shortcomings or limitations identified during the evaluation and error analysis phases. This may involve fine-tuning the model’s parameters, adjusting the training data or preprocessing steps, or exploring alternative model architectures. By iteratively improving the model based on feedback from the evaluation and error analysis, developers can enhance its performance and robustness in detecting defects.
Overall, model evaluation and validation play a critical role in ensuring the effectiveness and reliability of the defect detection system. By rigorously assessing the model’s performance, conducting error analysis, and iteratively refining the model, developers can create a defect detection system that meets the desired quality standards and effectively identifies defects in the given dataset.
Deployment and integration
Deployment and integration are crucial steps in the development lifecycle of an AI-powered defect detection system, involving the transition of the trained model from a development environment to a production environment where it can be used for real-world defect detection tasks. This phase ensures that the defect detection system is seamlessly integrated into existing workflows and systems, enabling its effective operation in production environments.
Firstly, deployment involves the process of deploying the trained model into production environments, making it accessible for use by end-users or other systems. This may involve packaging the model into a deployable format and deploying it on the appropriate infrastructure, such as cloud-based servers or edge devices. Additionally, developers may need to develop application programming interfaces (APIs) or interfaces that enable seamless integration of the model with existing quality control workflows and systems. These interfaces allow other systems or users to interact with the defect detection model, submit data for analysis, and receive predictions or feedback in real-time.
Furthermore, integration involves integrating the deployed model with existing quality control workflows and systems to ensure smooth operation and interoperability. This may involve connecting the defect detection system with production equipment, automation systems, or data management platforms to enable automated data collection, analysis, and decision-making. Integration also involves ensuring compatibility with existing data formats, protocols, and standards to facilitate seamless communication and data exchange between different systems.
Moreover, implementing real-time monitoring and feedback mechanisms is essential to continuously assess the performance of the deployed model and ensure its reliability and effectiveness in detecting defects. This involves monitoring key performance indicators (KPIs) such as model accuracy, false positive rate, and false negative rate in real-time and implementing mechanisms to alert users or trigger corrective actions if performance falls below acceptable thresholds. Additionally, collecting feedback from end-users and stakeholders and incorporating it into the defect detection system allows for ongoing optimization and refinement to improve its performance and reliability over time.
Overall, deployment and integration are critical phases in the development of an AI-powered defect detection system, ensuring its seamless transition from development to production environments and its effective operation within existing workflows and systems. By deploying the trained model, integrating it with existing systems, and implementing real-time monitoring and feedback mechanisms, developers can ensure the reliability, effectiveness, and scalability of the defect detection system in real-world applications.
Maintenance and continuous improvement
Maintenance and continuous improvement are essential aspects of managing an AI-powered defect detection system over its lifecycle, ensuring its effectiveness, reliability, and adaptability to changing conditions. This phase involves ongoing monitoring, feedback collection, model retraining, and staying abreast of advancements in AI and machine learning technologies.
Firstly, monitoring the performance of the deployed defect detection system is crucial to identify any deviations or degradation in its performance over time. This involves regularly assessing key performance indicators (KPIs) such as accuracy, precision, recall, and false positive rate and comparing them against predefined thresholds or benchmarks. Additionally, collecting feedback from users and stakeholders allows for gathering insights into the system’s usability, reliability, and effectiveness in real-world scenarios.
Furthermore, incorporating new data and insights into the training process enables the defect detection model to adapt to changes in production processes or defect patterns. This may involve periodically retraining the model using updated or augmented datasets to capture new trends, patterns, or variations in defect characteristics. By continuously refining the model based on the latest data and insights, developers can ensure that the defect detection system remains accurate and effective in detecting defects over time.
Moreover, staying updated with advancements in AI and machine learning technologies is essential for leveraging new techniques and algorithms to improve the defect detection system’s performance and efficiency. This involves keeping abreast of research developments, attending conferences, and engaging with the broader AI community to identify innovative approaches and best practices for defect detection. By incorporating cutting-edge techniques and algorithms into the defect detection system, developers can enhance their capabilities and stay ahead of the competition.
Overall, maintenance and continuous improvement play a critical role in maximizing the effectiveness and longevity of an AI-powered defect detection system. By monitoring performance, collecting feedback, incorporating new data and insights, and staying updated with advancements in AI, developers can ensure that the defect detection system remains reliable, accurate, and adaptable to evolving production processes and defect patterns.
Building an AI-powered defect detection system for quality control involves a series of technical steps, including data collection and preprocessing, feature extraction and engineering, model development and evaluation, deployment and integration, and maintenance and continuous improvement. By carefully addressing each of these steps and leveraging domain expertise and advanced machine learning techniques, organizations can develop effective defect detection systems that enhance product quality, reduce manufacturing costs, and improve overall operational efficiency.
Optimize Your Operations With AI Agents
Optimize your workflows with ZBrain AI agents that automate tasks and empower smarter, data-driven decisions.
Considerations for building AI-powered defect detection systems
Building AI-powered defect detection systems involves several considerations to ensure their effectiveness, reliability, and practicality in real-world applications. Here are key considerations for building such systems:
- Domain expertise: Understanding the specific domain or industry where the defect detection system will be deployed is essential. Domain experts possess valuable insights into the characteristics of defects, production processes, and quality standards, which are crucial for designing effective detection algorithms and models.
- Data availability and quality: High-quality training data is essential for building accurate and robust defect detection models. Considerations include the availability of labeled datasets containing examples of both defective and non-defective items, as well as the representativeness and diversity of the data to ensure the model generalizes well to new scenarios.
- Computational resources: Building and training AI-powered defect detection models can be computationally intensive, requiring sufficient computational resources such as powerful CPUs or GPUs, as well as adequate storage and memory. Considerations should be made for scaling up resources as needed to accommodate larger datasets or more complex models.
- Integration with existing workflows: AI-powered defect detection systems need to integrate with existing quality control workflows and systems seamlessly. Compatibility with existing production equipment, automation systems, and data management platforms is essential to ensure smooth deployment and operation of the system within the manufacturing environment.
- Cost-benefit analysis: Conducting a thorough cost-benefit analysis is crucial to assess the feasibility and return on investment of implementing AI-powered defect detection systems. Considerations include the initial investment in technology, training, and infrastructure, as well as the potential cost savings from reduced defects, improved product quality, and increased operational efficiency.
- Scalability and flexibility: AI-powered defect detection systems should be designed to scale and adapt to changing production requirements and evolving defect patterns. The system should be flexible enough to accommodate new types of defects, production processes, or product variants without requiring significant reengineering or retraining.
- Collaboration and expertise: Building AI-powered defect detection systems requires collaboration between data scientists, machine learning engineers, domain experts, and end-users. Leveraging the expertise of multidisciplinary teams ensures that the system addresses the specific needs and challenges of the industry and maximizes its effectiveness in defect detection.
- Ethical and regulatory compliance: Considerations should be made for ethical and regulatory compliance, particularly regarding data privacy, security, and bias mitigation. Adhering to ethical guidelines and regulatory requirements such as GDPR, HIPAA, or industry-specific standards ensures that the system operates ethically and responsibly while maintaining the trust of stakeholders.
- Continuous improvement and evaluation: AI-powered defect detection systems should be continuously monitored, evaluated, and improved over time. Implementing feedback loops for model performance evaluation, monitoring key performance metrics, and incorporating user feedback enable ongoing optimization and refinement of the system to ensure its long-term effectiveness and reliability.
Building AI-powered defect detection systems requires careful consideration of various factors, including domain expertise, data availability and quality, computational resources, integration with existing workflows, cost-benefit analysis, scalability and flexibility, collaboration and expertise, ethical and regulatory compliance, continuous improvement and evaluation. By addressing these considerations, organizations can develop AI-powered defect detection systems that effectively meet their quality control needs and drive improvements in product quality and operational efficiency.
How can LeewayHertz help in building AI-powered defect detection systems?
LeewayHertz stands out as a premier provider of AI consulting and development services, boasting extensive expertise in artificial intelligence and machine learning. With a team of seasoned professionals well-versed in advanced technologies, LeewayHertz offers unparalleled capabilities in developing AI-powered solutions tailored to meet diverse business needs.
LeewayHertz offers a comprehensive suite of services for building AI-powered defect detection systems, encompassing every stage of the development lifecycle. From problem definition and data collection to model development, deployment, and maintenance, LeewayHertz provides end-to-end support to ensure the successful implementation of defect detection solutions.
LeewayHertz has a proven track record of successful collaborations with clients across various industries in implementing AI solutions. One notable case study exemplifying LeewayHertz’s prowess is its collaboration with a global leader in manufacturing.
Facing challenges in detecting anomalies during their production processes, particularly occurrences leading to material wastage, the client collaborated with LeewayHertz to develop a cutting-edge computer vision-based anomaly detection system tailored for early anomaly detection.
Through this collaboration, LeewayHertz enabled the client to swiftly identify anomalies in real-time, thereby minimizing material wastage and optimizing operational efficiency. The computer vision-based system provided timely alerts, empowering operators to take immediate corrective action during the manufacturing process.
Partnering with LeewayHertz for AI projects offers several advantages. LeewayHertz boasts profound expertise in AI and ML technologies, guaranteeing the creation of robust and dependable AI solutions customized to meet the precise needs of businesses. Furthermore, LeewayHertz adopts a collaborative approach and remains dedicated to delivering tangible business outcomes, ensuring smooth project execution and maximizing customer satisfaction.
LeewayHertz’s AI development services for defect detection systems
At LeewayHertz, we design and develop custom AI solutions that transform defect detection across various industries. Our strategic AI/ML consulting enables organizations to leverage AI to achieve detection accuracy, streamlined operations, optimized production processes and enhanced product quality.
Our expertise in developing Proof of Concepts (PoCs) and Minimum Viable Products (MVPs) allows firms to test the potential impacts of AI tools in real-world scenarios, ensuring that the solutions are effective and tailored to each sector’s specific requirements.
Our work in generative AI transforms routine quality control tasks like visual inspections and data analysis, automating these processes to free up personnel for more strategic roles.
By fine-tuning large language models to the intricacies of industry-specific terminology and operational data, LeewayHertz enhances the accuracy and relevance of AI-driven analyses and defect detection.
Additionally, we ensure these AI systems integrate seamlessly with existing technological infrastructures, enhancing operational efficiency and decision-making in quality control operations.
Our AI solutions development expertise
AI solutions development for defect detection typically involves creating systems that automate identifying and analyzing potential defects across manufacturing, packaging, and assembly processes. These solutions integrate key technologies such as computer vision, data aggregation, and machine learning, which compile and analyze high volumes of operational data. This robust data foundation supports advanced analytics capabilities, allowing for the precise detection and classification of defects. These solutions often cover areas like real-time monitoring, predictive maintenance, compliance verification, and feedback loop optimization.
Overall, AI-powered defect detection systems aim to reduce waste, minimize downtime, and ensure product quality.
AI agent/copilot development for defect detection systems
LeewayHertz builds custom AI agents and copilots that enhance various operations in quality control, enabling companies to save time and resources while facilitating faster and more accurate decision-making. Here is how they help:
Advanced detection capabilities:
- Utilizing high-resolution imaging and AI to identify defects that are invisible to the human eye at high production speeds.
- Detecting and alerting on anomalous patterns that could indicate potential defects.
Process optimization:
- AI agents analyze defect data to recommend machine or process adjustments that can reduce the incidence of defects.
- Implementing systems that adapt and improve over time by learning from each detected defect, enhancing detection algorithms continually.
- Analyzing trends over time to predict when quality might deteriorate, allowing preemptive process adjustments.
Predictive and proactive maintenance:
- Predicting equipment failures that could lead to product defects helps schedule maintenance proactively to prevent downtime.
- Optimizing resource allocation by predicting defect trends and adjusting staffing and material use accordingly.
- Analyzing operational data to optimize machine settings, reducing wear and tear and extending the lifespan of critical equipment.
Compliance and standards enforcement:
- Continuously verify that production processes and products meet all relevant industry standards and regulations.
- Automate the creation and storage of quality control documentation, ensuring accuracy and accessibility for audits.
- Provide real-time alerts if production deviates from compliance norms, allowing immediate correction to avoid quality issues and regulatory penalties.
AI agents and copilots developed by LeewayHertz not only enhance the efficiency and effectiveness of defect detection processes but also significantly improve the strategic decision-making capabilities within quality control. By integrating these advanced AI solutions into their existing frameworks, companies across industries can achieve a substantial competitive advantage, navigating the complex landscape of quality assurance with innovative, efficient, and reliable AI-driven tools and strategies. This leads to significantly reduced defect rates, optimized production processes, and consistently high-quality products.
Industries and domains benefiting from building AI-powered defect detection systems
Industries and domains across various sectors benefit significantly from the implementation of AI-powered defect detection systems. Here’s an overview of some of the industries and domains where these systems have a profound impact:
- Manufacturing: In manufacturing industries such as automotive, electronics, aerospace, and consumer goods, AI-powered defect detection systems ensure the production of high-quality products by identifying defects in components, assemblies, and finished goods. These systems improve product reliability, reduce manufacturing costs, and enhance customer satisfaction.
- Pharmaceuticals and healthcare: In pharmaceutical manufacturing, AI-powered defect detection systems play a crucial role in ensuring the safety and efficacy of pharmaceutical products. These systems detect defects in drug formulations, packaging, and labeling, preventing the distribution of defective or potentially harmful medications. In healthcare, AI-powered defect detection systems are used in medical imaging to identify abnormalities in X-rays, MRIs, and CT scans, aiding in the diagnosis and treatment of diseases.
- Food and beverage: In the food and beverage industry, AI-powered defect detection systems are employed to ensure food safety and quality. These systems detect contaminants, foreign objects, and quality defects in food products, preventing contaminated or substandard products from reaching consumers. AI-powered defect detection systems also help food manufacturers comply with regulatory standards and prevent foodborne illnesses.
- Textiles and apparel: In the textile and apparel industry, AI-powered defect detection systems are used to inspect fabrics, garments, and finished textile products for defects such as tears, stains, or misprints. These systems ensure the production of high-quality textiles and apparel, reduce waste and improve production efficiency.
- Semiconductors and electronics: In the semiconductor and electronics industry, AI-powered defect detection systems are employed to detect defects in semiconductor wafers, integrated circuits (ICs), printed circuit boards (PCBs), and electronic components. These systems ensure the reliability and performance of electronic devices, reduce production costs, and improve yield rates.
- Packaging and printing: In the packaging and printing industry, AI-powered defect detection systems are used to inspect packaging materials, labels, and printed products for defects such as misprints, smudges, or registration errors. These systems ensure the accuracy and quality of packaging and printed materials, reduce waste, and improve production efficiency.
- Automotive and transportation: In the automotive and transportation industry, AI-powered defect detection systems are employed to inspect vehicle components, assemblies, and finished vehicles for defects such as scratches, dents, or paint imperfections. These systems ensure the quality and safety of vehicles, reduce manufacturing costs and enhance customer satisfaction.
- Construction and infrastructure: In the construction and infrastructure industry, AI-powered defect detection systems are used to inspect building materials, structural components, and infrastructure projects for defects such as cracks, corrosion, or structural weaknesses. These systems ensure the safety and durability of buildings and infrastructure, reduce maintenance costs, and prevent accidents.
AI-powered defect detection systems have a wide range of applications across industries and domains, ensuring the production of high-quality products, improving safety and reliability, reducing costs, and enhancing customer satisfaction. These systems play a crucial role in quality assurance, regulatory compliance, and risk management, driving efficiency and innovation in various sectors of the economy.
Future trends and innovations in AI-powered defect detection systems
AI-powered defect detection systems continue to evolve rapidly, driven by advancements in technology and the increasing demand for higher quality standards across industries. Here’s an exploration of future trends and innovations shaping the landscape of defect detection:
- Emerging technologies shaping the future of defect detection: Emerging sensing technologies, such as hyperspectral imaging and IoT integration, are enhancing defect detection capabilities. Augmented reality (AR) and virtual reality (VR) technologies provide immersive visualization for defect identification, while edge computing enables real-time processing closer to the data source.
- Potential advancements in AI algorithms and architectures: Advancements in explainable AI (XAI) techniques improve the interpretability of defect detection models. Federated learning facilitates collaborative training across distributed data sources, while continual learning enables models to adapt to evolving production conditions. Graph neural networks (GNNs) enhance the ability to detect complex relationships in defect detection tasks.
- Predictions for the evolution of quality control practices: AI-powered defect detection systems will drive predictive maintenance and quality control practices by analyzing historical defect data. Autonomous quality control systems will autonomously monitor, detect, and classify defects, reducing reliance on manual inspection. Integration with digital twins will enable virtual simulation and optimization of production processes, while customization and personalization will tailor defect detection capabilities to specific industry needs.
Future trends and innovations in AI-powered defect detection systems hold the promise of enhancing defect detection capabilities, improving product quality, and driving operational efficiency in manufacturing environments.
Endnote
The development and implementation of AI-powered defect detection systems represent a transformative leap in quality control processes across various industries. Through the utilization of advanced machine learning algorithms, these systems offer unparalleled accuracy, efficiency, and adaptability in identifying and categorizing defects in manufactured products. By harnessing the power of AI, companies can streamline their quality assurance processes, reduce production costs, and enhance overall product quality.
Throughout this article, we have explored the key components and considerations involved in building effective AI-powered defect detection systems. From data collection and preprocessing to model selection and evaluation, each stage plays a crucial role in ensuring the success of these systems. Additionally, we have discussed the importance of domain expertise, labeled data, and continuous learning in refining and optimizing the performance of defect detection models.
Moreover, we have highlighted the potential challenges and limitations associated with AI-powered defect detection, including the need for large and diverse datasets, model interpretability, and the risk of false positives and negatives. Addressing these challenges requires a collaborative effort between data scientists, domain experts, and stakeholders to develop robust solutions that meet the specific needs and requirements of each application.
Looking ahead, the future of AI-powered defect detection systems is promising, with ongoing advancements in machine learning techniques, sensor technologies, and computational resources. As these technologies continue to evolve, we can expect even greater accuracy, efficiency, and scalability in defect detection across various industries. Ultimately, by embracing AI-powered solutions, companies can enhance their competitiveness, drive innovation, and deliver higher-quality products to consumers worldwide.
Ready to redefine your quality control processes with AI-powered defect detection systems? Contact LeewayHertz for expert AI consulting and development services tailored to your specific needs, and take the first step towards optimizing your production efficiency and product quality today.
Start a conversation by filling the form
All information will be kept confidential.