AI for production planning: Significance, use cases, benefits, technologies and development
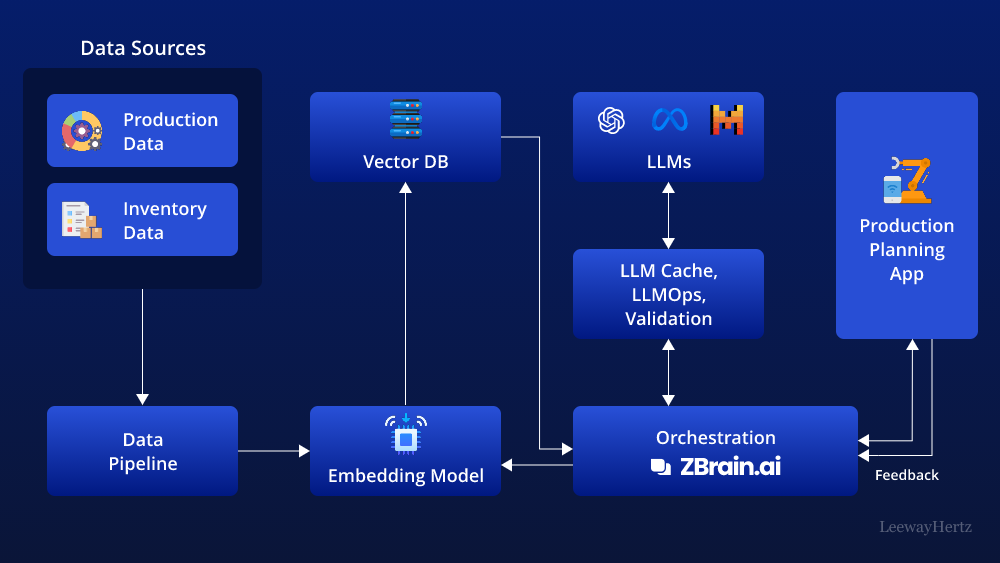
AI transforms production planning and scheduling by leveraging advanced algorithms and data analytics to optimize decision-making, improve efficiency, and adapt to dynamic production environments.
In the modern manufacturing, where customer demands shift rapidly and market forces are ever-evolving, two pivotal processes form the cornerstone of operational success: Production planning and scheduling. These processes are essential for aligning manufacturing activities with business objectives, ensuring that resources are efficiently allocated and products are delivered on time. However, in an era of relentless pursuit of excellence and innovation, traditional methods of production planning and scheduling are encountering new challenges. These once-reliable approaches, now tested by the complexities of today’s manufacturing landscape, prompt a reevaluation of strategies to stay ahead in a competitive market.
Have you ever wondered why production lines experience unexpected downtime, customer delivery deadlines are missed, or inventory costs skyrocket? These common challenges in the manufacturing industry often result from outdated production planning strategies struggling to adapt to a rapidly evolving world. Enter Artificial Intelligence (AI), a transformative force redefining these traditional processes.
Imagine a future where manufacturing operates seamlessly with agile production lines that respond to market shifts, optimized resource allocation, and precise demand forecasting. This future is not a distant dream but a reality already unfolding, thanks to AI’s transformative power. AI is reshaping manufacturing, replacing rigid production processes and static schedules with intelligent systems that respond, anticipate, learn, and self-optimize at unprecedented speeds.
Today’s production planners and manufacturers face a profound shift as AI technologies empower smarter decisions, optimized resource allocation, and schedules that align seamlessly with real-world dynamics.
This article delves into the intricacies of AI in production planning and scheduling, highlighting its pivotal role in modern manufacturing. We will explore the challenges faced by professionals, the compelling reasons for integrating AI, the remarkable benefits it brings, and the advanced AI technologies redefining the field.
- An overview of production planning and scheduling
- How does AI in production planning work?
- Challenges in production planning and scheduling stages and how AI addresses them?
- Streamlining production planning workflow with GenAI
- Use cases and applications of AI in production planning and scheduling
- Benefits of AI in production planning and scheduling
- How LeewayHertz’s generative AI platform optimizes production planning and scheduling workflows?
- LeewayHertz’s AI development services for production planning
- Future trends in AI-enhanced production planning and scheduling
An overview of production planning and scheduling
Production planning and scheduling are critical functions within manufacturing and operations management. They involve the process of organizing and optimizing resources to produce goods efficiently or deliver services while meeting customer demand and maintaining cost-effectiveness.
AI transforms production planning and scheduling by leveraging advanced algorithms and data analytics to optimize decision-making, improve efficiency, and adapt to dynamic production environments.
AI enhances demand forecasting in production planning by analyzing historical data and market trends more accurately. It optimizes Master Production Scheduling (MPS) by considering various factors like demand forecasts, resource availability, and production constraints, generating flexible plans that adapt to changes. Furthermore, AI-driven Material Requirement Planning (MRP) systems optimize inventory levels by analyzing real-time data and predicting future material needs more accurately, thus minimizing stockouts and holding costs. In addition, cost-cut capacity planning benefits from AI simulations, identifying constraints and offering resource allocation recommendations for a feasible plan. Moreover, AI algorithms in finite capacity scheduling optimize production schedules, considering complex constraints like machine capabilities and labor availability to maximize resource utilization.
AI automates work order generation in production scheduling based on priorities, resource availability, and constraints. It optimizes task sequencing to minimize idle time and setup costs by considering job dependencies and machine capabilities. AI algorithms achieve load balancing by distributing workloads evenly among machines and workers to optimize resource usage. Lastly, AI systems monitor production data in real-time, making adjustments as needed to handle disruptions such as machine breakdowns or changes in demand, ensuring smooth production flow.
How-does-AI-in-production-planning-work
Integrating AI into production planning optimizes data analysis, generates actionable insights, and enhances the decision-making process. It transcends traditional production planning processes by leveraging advanced large language models (LLMs) and connecting them with an organization’s unique operational data. It unlocks new levels of insight generation, enabling businesses to make data-driven decisions in real time and improve overall efficiency.
This architecture leverages various components to streamline the production planning process. Here’s a step-by-step breakdown of how it works:
Data sources: The process begins by gathering data from various sources relevant to production planning. This data can include:
- Production data: Information about manufacturing processes, machine performance, and production schedules from internal systems.
- Inventory data: Data on raw materials, work-in-progress, and finished goods inventory levels from inventory management systems.
- Supply chain data: Insights into supplier performance, lead times, and delivery schedules from supply chain management systems.
- Demand forecasts: Projections of future product demand based on historical sales data, market trends, and customer orders.
- Operational data: Information related to workforce availability, maintenance schedules, and operational constraints.
- External factors: Data on external factors such as market conditions, and industry trends.
Data pipelines: Data from the above sources are then routed through data pipelines. These pipelines handle data ingestion, cleaning, and structuring, preparing it for further analysis.
Embedding model: The prepared data is then processed by an embedding model. This model converts the textual and numerical data into representations called vectors that AI models can understand. Popular embedding models include those from OpenAI, Google, and Cohere.
Vector database: The generated vectors are stored in a vector database, allowing for efficient querying and retrieval. Examples of prominent vector databases include Pinecone, Weaviate, and PGvector.
APIs and plugins: APIs and plugins like Serp, Zapier, and Wolfram play a crucial role by connecting different components and enabling additional functionalities, such as accessing extra data, connecting to LLMs or performing specific tasks easily.
Orchestration layer: The orchestration layer is critical in managing the workflow. ZBrain is an example of this layer that simplifies prompt chaining, manages interactions with external APIs by determining when API calls are required, retrieves contextual data from vector databases, and maintains memory across multiple LLM calls. Ultimately, this layer generates a prompt or series of prompts submitted to a language model for processing. The role of this layer is to orchestrate the flow of data and tasks, ensuring seamless coordination across all components within the AI-based production planning architecture.
Query execution: The data retrieval and generation process begins when the user submits a query to the production planning app. This query can be about anything relevant to production planning, such as production schedules, inventory levels, or supply chain performance.
LLM processing: Once received, the app transmits the query to the orchestration layer. This layer retrieves relevant data from the vector database and LLM cache and then sends it to the appropriate LLM for processing. The choice of LLM depends on the nature of the query.
Output: The LLM generates an output based on the query and the data it receives. This output can take various forms, such as production schedules, inventory forecasts, or supply chain performance reports.
Production planning app: The validated output is then presented to the user through the production planning app. This is the core application where all the data, analysis, and insights converge. It presents the findings in a user-friendly format for decision-makers, enabling them to optimize production processes and improve overall efficiency.
Feedback loop: User feedback on the LLM’s output is crucial to this architecture. The feedback is used to improve the accuracy and relevance of the LLM output over time.
Agent: AI agents are another significant part of this process that addresses complex problems, interacts with the external environment, and enhances learning through post-deployment experiences. They achieve this by employing advanced reasoning and planning, utilizing strategic tools, and leveraging memory, recursion, and self-reflection.
LLM cache: Tools like Redis, SQLite, or GPTCache are used to cache frequently accessed information, speeding up the response time of the AI system.
Logging/LLMOps: Throughout this process, LLM operations (LLMOps) tools like Weights & Biases, MLflow, Helicone, and Prompt Layer help log actions and monitor performance. This ensures the LLMs are functioning optimally and continuously improve through feedback loops.
Validation: A validation layer is employed to validate the LLM’s output. This is done through tools like Guardrails, Rebuff, Guidance, and LMQL to ensure the accuracy and reliability of the information provided.
LLM APIs and hosting: LLM APIs and hosting platforms are essential for executing production planning tasks and hosting the application. Depending on the requirements, developers can select from LLM APIs provided by companies such as OpenAI and Anthropic or opt for open-source models. Similarly, they can choose hosting platforms from cloud providers like AWS, GCP, Azure, and Coreweave or opt for opinionated clouds like Databricks, Mosaic, and Anyscale. The choice of LLM APIs and cloud hosting platforms depends on the project’s needs and developers’ preferences.
This structured flow provides a detailed overview of how AI facilitates production planning, leveraging various data sources and technological tools to generate accurate and actionable insights. Overall, AI automates various tasks involved in production planning, improves efficiency, and enables a more comprehensive analysis of operational data.
Optimize Your Operations With AI Agents
Optimize your workflows with ZBrain AI agents that automate tasks and empower smarter, data-driven decisions.
Challenges in production planning and scheduling stages and how AI addresses them?
Production planning and scheduling involve several stages to ensure the efficient and timely execution of manufacturing processes. The specific stages might differ depending on the industry and the complexity of the production process. However, the following are common stages in production planning and scheduling, each presenting its own set of challenges. AI technologies offer innovative solutions to address these challenges effectively:
Demand forecasting
Challenge: Forecasting demand poses a significant challenge due to the inherent uncertainties of market trends and external variables. Fluctuations in consumer behavior, economic conditions, or unforeseen events complicate the accurate prediction of future demand. This unpredictability can lead to inventory surplus or shortages, impacting the efficiency of the supply chain.
Solution: To address the challenge, AI deploys advanced algorithms capable of processing large and diverse datasets. These algorithms analyze historical patterns and incorporate real-time data and external variables, such as social trends. By continuously adapting to changing conditions, AI enhances the accuracy of demand forecasts, providing businesses with more reliable insights. This adaptability is crucial for navigating the dynamic nature of markets and improving overall supply chain efficiency.
Sales and Operations Planning (S&OP)
Challenge: The main challenge in Sales and Operations Planning (S&OP) lies in the complexity of coordinating across multiple departments and ensuring alignment between production plans and sales forecasts. Achieving synergy among diverse teams and functions can be intricate, and discrepancies can lead to inefficiencies, excess inventory, or production shortfalls.
Solution: AI addresses this challenge by facilitating for cross-functional collaboration. Through real-time data visibility, AI enables seamless communication and information sharing among departments. This guarantees that decision-makers have access to the most up-to-date information, fostering synchronized decision-making. AI’s ability to analyze vast datasets aids in identifying patterns and trends, further enhancing the accuracy of decisions in the sales and operations planning process. This collaborative and data-driven approach improves overall operational efficiency and helps organizations adapt swiftly to changing market dynamics.
Master Production Scheduling (MPS)
Challenge: Balancing production quantities and timelines while considering constraints posed by limited resources presents a significant challenge in Master Production Scheduling (MPS). Achieving an optimal balance is intricate, as overproduction can lead to excess inventory, while underproduction can result in unmet customer demands.
Solution: AI addresses this challenge through optimization algorithms that take into account multiple factors. These algorithms analyze resource availability, fluctuations in demand, and cost constraints to generate a master production schedule that maximizes efficiency. By considering these variables simultaneously, AI ensures that the production plan aligns with available resources, minimizes costs, and meets customer demand effectively. This AI-driven approach not only optimizes scheduling but also contributes to enhanced overall operational performance and adaptability to dynamic production environments.
Material Requirement Planning (MRP)
Challenge: The complexity of Material Requirement Planning (MRP) lies in managing intricate supply chains, where potential disruptions can impact the availability of materials essential for production. Unforeseen events, delays, or shortages can result in production delays and inefficiencies.
Solution: AI addresses this challenge through enhanced MRP systems that leverage predictive analytics. By analyzing historical data, market trends, and external variables, AI predicts potential disruptions in the supply chain. This proactive approach allows businesses to anticipate challenges and implement strategies to mitigate their impact, ensuring the consistent availability of materials when needed. AI-driven MRP systems contribute to a more resilient and adaptive supply chain, reducing the risk of production disruptions and optimizing the overall efficiency of material management processes.
Capacity planning
Challenge: Capacity planning involves aligning production plans with the actual capacity of facilities and the workforce. Balancing production demand with available resources is crucial to avoid inefficiencies like overloading or underutilization.
Solution: AI addresses this challenge through advanced capacity planning tools that leverage historical production data and analyze workforce capabilities. By considering variables such as production demand, resource availability, and workforce efficiency, AI-driven tools optimize production plans. These tools help prevent overloads that could lead to bottlenecks and delays, as well as underutilization that may result in wasted resources. The adaptive nature of AI ensures that capacity planning is dynamic, allowing businesses to adjust plans in real-time to meet changing demands and optimize resource utilization.
Routing
Challenge: Routing involves determining the most efficient sequence of operations for each product, considering factors like machine capabilities, production costs, and time constraints. Finding the optimal path for production processes is crucial for overall efficiency.
Solution: AI addresses this challenge through algorithms that optimize routing. These algorithms analyze various factors, including machine capabilities and production costs, to determine the most efficient sequence of operations. By considering multiple variables simultaneously, AI ensures that the routing of products is optimized for efficiency, contributing to a streamlined and cost-effective production flow.
Scheduling
Challenge: Creating a detailed schedule that considers multiple tasks, dependencies, and constraints poses a significant challenge. The complexity of managing various elements in a schedule, including resource allocation and task sequencing, can lead to inefficiencies and delays.
Solution: AI-based scheduling tools provide a solution by optimizing task sequencing, resource allocation, and timeline management. These tools adapt to real-time changes, allowing for dynamic adjustments to the schedule. By leveraging AI, businesses can create schedules that are not only efficient but also resilient to changes, ensuring optimal resource utilization and timely task completion.
Loading
Challenge: The challenge in loading is to efficiently assign workloads to each work center based on its capacity and capability, ensuring a balanced utilization of resources to prevent overloading or underutilization.
Solution: AI addresses this challenge through sophisticated algorithms that optimize resource allocation. These algorithms analyze factors such as work center capacity, task requirements, and overall production demands to ensure an optimal distribution of workloads. By preventing overloading and underutilization, AI-driven loading contributes to a more efficient production process and maximizes the use of available resources.
Dispatching
Challenge: Dispatching involves lies in effectively communicating the schedule and ensuring the timely initiation of production processes. Efficient coordination is crucial for minimizing delays and maintaining a smooth workflow.
Solution: AI-enhanced dispatching systems provide a solution by automating communication processes. These systems offer real-time updates to workers, ensuring they have the latest schedule information. By automating the initiation of production processes through timely work order execution, AI enhances efficiency and responsiveness, reducing the risk of delays and improving overall production performance.
Monitoring and control
Challenge: The challenge in monitoring and control lies in the real-time identification and resolution of disruptions or delays in the production process, which is essential for maintaining efficiency and preventing potential bottlenecks.
Solution: AI addresses this challenge through systems equipped with real-time monitoring capabilities. These AI systems analyze production data in real time, offering insights for quick decision-making. By enabling proactive adjustments to the production process, AI helps prevent or minimize disruptions, contributing to a more agile and responsive manufacturing environment.
Feedback and continuous improvement
Challenge: The challenge in feedback and continuous improvement involves effectively gathering and analyzing feedback to continually enhance processes and ensure that production evolves to meet changing conditions and demands.
Solution: AI analytics tools provide a solution by systematically analyzing performance data. These tools identify trends, patterns, and areas for improvement, offering actionable insights for continuous enhancement. By supporting data-driven decision-making, AI contributes to the refinement of production processes over time, fostering a culture of continuous improvement within the organization.
AI solutions play a pivotal role in addressing these challenges by leveraging advanced analytics, machine learning, and optimization algorithms to enhance the efficiency and effectiveness of production planning and scheduling processes.
Streamlining production planning workflow with GenAI
Generative AI transforms production planning by creating precise forecasts and optimizing resource allocation. It enables manufacturers to respond quickly to changing demands, reducing waste and enhancing overall efficiency. Let’s understand in detail the role of generative AI in each step of the production planning workflow.
Demand forecasting
Steps Involved | Sub-Steps Involved | Role of GenAI |
---|---|---|
Data Collection |
|
|
Demand Analysis |
|
|
Capacity Planning |
|
|
Material requirement and resource allocation
Steps Involved | Sub-Steps Involved | Role of GenAI |
---|---|---|
Procurement Planning and Optimization |
|
|
Allocate Resources |
|
|
Risk Assessment |
|
|
Production scheduling
Steps Involved | Sub-Steps Involved | Role of GenAI |
---|---|---|
Manage Resource |
|
|
Execute Production |
|
|
Monitor Performance |
|
|
Quality control
Steps Involved | Sub-Steps Involved | Role of GenAI |
---|---|---|
Inspect Product |
|
|
Analyze Performance |
|
|
Implement Corrective Action |
|
|
Supply chain management
Steps Involved | Sub-Steps Involved | Role of GenAI |
---|---|---|
Plan Logistics |
|
|
Manage Inventory |
|
|
Use cases and applications of AI in production planning and scheduling
AI is transforming production planning with its ability to analyze vast amounts of data and make real-time adjustments, driving efficiency and cost savings. Manufacturers can streamline operations and enhance overall productivity by leveraging advanced algorithms for tasks such as demand forecasting, inventory optimization, and dynamic scheduling. Key use cases and applications of AI in production planning include:
Demand forecasting
AI algorithms leverage extensive historical sales data, current market trends, and external factors to produce precise demand forecasts. This allows manufacturers to proactively anticipate shifts in customer preferences or market conditions and adjust their production plans. Enhanced accuracy in demand forecasting helps minimize the risks of overproduction or stockouts, leading to more efficient inventory management and reduced costs.
Dynamic production planning
AI optimizes Master Production Scheduling (MPS) by integrating real-time data such as demand fluctuations, resource availability, and production constraints. By continuously analyzing and adjusting production plans, AI ensures that manufacturing processes remain agile and responsive to changes. This dynamic approach helps balance production schedules with actual market demands, reducing downtime and improving overall efficiency.
Inventory optimization
AI-driven Material Requirement Planning (MRP) systems analyze detailed data on material usage patterns, supplier lead times, and performance metrics to fine-tune inventory levels. By predicting material needs more accurately, these systems reduce excess inventory and holding costs while ensuring that materials are available when required. This optimization supports smoother production processes and minimizes disruptions caused by inventory shortages.
Capacity planning and optimization
AI uses simulation models to assess production scenarios and identify potential capacity constraints. By evaluating factors such as machine capabilities, labor availability, and production priorities, AI helps in optimal resource allocation. This enables manufacturers to maximize production capacity, reduce idle times, and streamline operations, ultimately enhancing overall productivity and efficiency.
Production scheduling
AI-based scheduling algorithms manage complex production constraints, including machine capabilities, setup times, and order priorities. These algorithms generate optimized production schedules that reduce the time required to complete orders (makespan), cut setup costs, and increase resource utilization. This results in improved throughput, reduced operational costs, and a more efficient production process.
Predictive maintenance
AI analyzes data from machine sensors to forecast potential equipment failures before they occur. Manufacturers can proactively manage maintenance needs by using predictive maintenance schedules informed by AI forecasts. This approach helps prevent unexpected equipment failures, reducing unplanned downtime and minimizing production disruptions. It enhances operational efficiency, prolongs equipment lifespan, and ensures a smoother production flow.
Real-time adjustment
AI systems continuously monitor production data and make real-time adjustments to the production schedule. This includes adapting to unexpected events such as rush orders, equipment malfunctions, or sudden changes in demand. By dynamically adjusting the schedule, AI helps maintain a consistent production flow, ensure timely delivery and minimize the impact of disruptions on overall operations.
Quality control and inspection
AI-powered image recognition technologies inspect products on the production line for defects and inconsistencies. These systems detect anomalies with high precision and provide immediate feedback, allowing for quick corrective actions. Enhanced quality control reduces the need for rework, improves product quality, and helps maintain high standards throughout manufacturing.
Supplier performance monitoring
AI evaluates supplier performance through detailed analysis of delivery reliability, quality metrics, and lead times. By monitoring these factors, manufacturers can make informed supplier selection and management decisions. This ensures a steady and reliable supply of materials, reduces the risk of delays, and enhances the overall efficiency of the supply chain.
Energy consumption optimization
AI algorithms assess production data to identify opportunities for energy savings. Manufacturers can lower energy costs and reduce their environmental footprint by optimizing machine usage and scheduling energy-intensive processes during off-peak hours. This helps reduce costs and aligns with sustainability goals and regulatory requirements.
Just-in-Time (JIT) inventory management
AI optimizes JIT inventory by synchronizing material deliveries with production schedules. This approach minimizes inventory holding costs and ensures that materials arrive exactly when needed for production. By reducing excess inventory, manufacturers can lower storage costs and improve cash flow while maintaining efficient production processes.
Production line balancing
AI algorithms analyze production line tasks to optimize the distribution of workloads across various stations. This balancing reduces bottlenecks, minimizes idle time, and ensures production lines operate efficiently. By achieving a more balanced workload, manufacturers can increase throughput, shorten cycle times, and enhance production efficiency.
Order prioritization
AI systems prioritize customer orders based on profitability, urgency, and available production capacity. This ensures that high-priority orders are processed and fulfilled promptly while maximizing profitability. Effective order prioritization improves customer satisfaction and optimizes the use of production resources.
Resource allocation in multi-site operations
AI optimizes resource allocation across multiple production sites by considering transportation times, production capacities, and inventory levels. This approach helps reduce transportation costs, balance production loads, and ensure efficient resource use across different locations. By coordinating resources effectively, manufacturers can achieve cost savings and operational efficiency.
Batch size optimization
AI algorithms determine optimal batch sizes by analyzing factors such as production costs, setup times, and demand variability. By dynamically adjusting batch sizes, manufacturers can minimize inventory levels, reduce production lead times, and optimize resource use. This leads to cost savings and a more responsive production process.
Forecasting seasonal demand
AI utilizes historical sales data and external factors, to forecast seasonal demand with greater accuracy. Manufacturers can adjust their production schedules and inventory levels by anticipating seasonal fluctuations. This proactive approach helps meet seasonal demand without overproducing or experiencing stockouts.
Optimizing production mix
AI evaluates factors such as demand patterns, product profitability, and production constraints to optimize the production mix. By selecting and sequencing products effectively, manufacturers can allocate production resources more efficiently, maximizing overall profitability and improving operational performance.
Automated order fulfillment
AI automates the order fulfillment process by routing orders to the most suitable production facilities based on criteria like capacity, location, and shipping costs. This ensures timely and cost-effective order completion, enhancing customer satisfaction and operational efficiency through reduced manual intervention and more streamlined logistics.
Employee scheduling and workforce management
AI optimizes employee schedules by considering workload, individual skills, and labor regulations. This ensures that the workforce effectively aligns with production demands, minimizing overtime costs and improving labor resource utilization. Efficient scheduling leads to better operational efficiency and employee satisfaction.
Automated material handling
AI-driven systems transform material handling by automating tasks such as sorting, transporting, and storing materials within the production facility. These systems use advanced robotics, sensors, and machine learning algorithms to efficiently move materials between different stages of production efficiently, reducing the need for manual labor and well as human error. By automating these processes, manufacturers can achieve higher throughput, reduce operational costs, and streamline workflows, resulting in faster production cycles and enhanced overall efficiency.
Production simulation
AI enables the creation of detailed simulations of production processes, allowing manufacturers to model various scenarios and assess their potential impact before implementation. By using AI to simulate different production strategies, resource allocations, and operational changes, companies can identify potential bottlenecks, optimize workflows, and make data-driven decisions to improve efficiency. This proactive approach helps in refining production plans, mitigating risks, and ensuring that new strategies are robust and well-suited to meet production goals.
Supply chain risk management
AI can be leveraged for comprehensive supply chain risk assessment and mitigation by analyzing a wide range of external factors. By integrating this data, AI systems can predict potential disruptions and recommend proactive measures to minimize impact, ensuring a more resilient and reliable supply chain.
Sustainability optimization
AI can be leveraged to optimize production planning for overall sustainability, focusing on water usage, waste reduction, and carbon footprint minimization. By analyzing data on resource consumption and emissions, AI can help companies implement more efficient processes and sustainable practices, ultimately reducing their environmental impact.
Collaborative planning
AI can enhance collaboration between departments such as sales, operations, and finance by integrating data and insights across functions. For instance, it can align production plans with sales forecasts and financial goals, ensuring that all departments work towards unified business objectives. This leads to improved coordination, more accurate planning, and better overall business performance.
Regulatory compliance
AI can ensure that production plans comply with various regulations and standards, particularly in highly regulated industries. By analyzing production processes and cross-referencing them with relevant legal and industry standards, AI helps identify and rectify compliance issues, ensuring adherence to all necessary regulations and minimizing the risk of violations.
Optimize Your Operations With AI Agents
Optimize your workflows with ZBrain AI agents that automate tasks and empower smarter, data-driven decisions.
Benefits of AI in production planning and scheduling
The adoption of AI in production planning and scheduling brings numerous benefits to manufacturing companies, helping them enhance efficiency, reduce costs, and improve overall operational performance. Some of the key benefits include:
- Improved accuracy: AI-driven systems can analyze vast amounts of data with precision, resulting in more accurate production schedules. This reduces the likelihood of overproduction, stockouts, or scheduling errors.
- Real-time adjustments: AI systems can adapt schedules in real-time, responding to unexpected events such as machine breakdowns, supply chain disruptions, or changes in demand. This agility minimizes disruptions and maintains production efficiency.
- Optimized resource utilization: Artificial Intelligence meticulously assesses the availability and capacity of essential resources such as machinery, labor, and materials, facilitating their strategic allocation. This approach leads to maximized utilization efficiency of resources, significantly reducing instances of idle time and ensuring a streamlined operational workflow.
- Enhanced productivity: By streamlining production processes and reducing downtime, AI boosts overall productivity. It enables manufacturers to produce more in less time, which can lead to cost savings.
- Cost reduction: AI helps in minimizing production costs by optimizing resource allocation, reducing waste, and improving energy efficiency. Lower operational costs contribute to increased profitability.
- Customization and flexibility: AI-driven systems can accommodate product customization and adapt to changes in customer demands. This flexibility enables manufacturers to meet specific customer requirements efficiently.
- Improved quality control: AI has the capability to oversee and regulate product quality at every stage of the production process. This ensures that products meet the desired quality standards, reducing rework and scrap.
- Forecasting accuracy: AI leverages historical data and predictive analytics to improve demand forecasting. This allows manufacturers to anticipate fluctuations in demand and adjust schedules accordingly.
- Scenario analysis: AI systems enable manufacturers to explore various “what-if” scenarios. This helps in evaluating the impact of different decisions on production schedules and making informed choices.
- Better decision-making: AI provides data-driven insights that support decision-making in production planning and scheduling. It offers recommendations for optimizing schedules and resource allocation.
- Reduced lead times: AI can optimize production schedules to minimize lead times, ensuring that products are delivered to customers faster. This can improve customer satisfaction and competitiveness.
- Resilience to disruptions: AI-equipped systems can proactively address and mitigate disruptions, such as supply chain issues or machine breakdowns. This enhances operational resilience and business continuity.
- Strategic planning: AI-driven solutions contribute to long-term strategic planning. They help manufacturers align production schedules with broader business goals and objectives.
- Competitive advantage: Manufacturers using AI in production planning and scheduling gain a competitive edge. They can deliver products faster, meet changing customer demands, and maintain cost-effective operations.
- Sustainability: AI can help reduce energy consumption and waste, contributing to more sustainable and environmentally friendly manufacturing practices.
- Adherence to regulations: AI can ensure that production schedules comply with industry-specific regulations and standards, reducing the risk of compliance issues.
The integration of AI in production planning and scheduling enhances efficiency, reduces costs, improves quality, and provides manufacturers with the agility to adapt to dynamic production environments. These benefits collectively contribute to increased competitiveness and profitability in the manufacturing industry.
How LeewayHertz’s generative AI platform optimizes production planning and scheduling workflows?
LeewayHertz’s generative AI platform, ZBrain, serves as a potent resource for manufacturing enterprises seeking to streamline production planning and scheduling processes, ultimately fostering operational efficiency and business growth. ZBrain empowers enterprises to create customized LLM-based applications, allowing them to fine-tune workflows, elevate customer interactions, and boost production planning operations. ZBrain facilitates the development of applications by leveraging advanced language models such as GPT-4, Vicuna, Llama 2, and GPT-NeoX. These models demonstrate adaptability to diverse data formats, encompassing text, images, and documents. The resulting applications contribute to informed decision-making, provide in-depth insights, and enhance productivity, all while adhering to stringent data privacy standards.
In the realm of production planning and scheduling, challenges like suboptimal forecasting accuracy, resource allocation inefficiencies, and prolonged decision-making processes are prevalent. ZBrain effectively confronts these challenges through its specialized Flow feature, offering an intuitive interface that facilitates seamless business logic creation without the need for coding skills. The platform effortlessly integrates various large language models, prompt templates, and media models, providing a user-friendly experience through drag-and-drop tools for the development and modification of sophisticated, intelligent applications.
Harnessing the power of AI-driven automation and advanced data analysis, these flows play a transformative role in converting intricate production data into actionable insights. This results in heightened efficiency, minimized error rates, and elevated overall production quality, presenting holistic solutions to some of the key challenges encountered in the production planning and scheduling domain within the manufacturing industry. Here is an example –
AI-driven production planning and optimization
ZBrain transforms production planning and optimization challenges for manufacturing enterprises by employing a secure and automated process. Through ZBrain Flow, it securely collects and analyzes sensitive information like production history, demand forecasts, and machine downtime. This confidential information undergoes an automated Exploratory Data Analysis (EDA) to extract meaningful insights, preserving the privacy of sensitive details. ZBrain’s adept parsing and structuring of reports ensures the final production plan is meticulously generated, incorporating private data to streamline processes such as resource allocation and production scheduling for optimal results while maintaining data privacy. The LLM-based apps developed using ZBrain enhance planning accuracy, optimize resource allocation, and streamline production scheduling, leading to notable advantages for businesses, including heightened operational efficiency, reduced waste, and improved resource utilization. Explore this flow to comprehend how ZBrain facilitates a more agile and efficient production planning process, adapting swiftly to market demands and ensuring optimal productivity.
Optimize Your Operations With AI Agents
Optimize your workflows with ZBrain AI agents that automate tasks and empower smarter, data-driven decisions.
LeewayHertz’s AI development services for production planning
At LeewayHertz, we specialize in developing customized AI solutions tailored to the specific needs of production planning. Our strategic AI/ML consulting empowers production teams to leverage AI for more informed decision-making, enhanced operational efficiency, and optimized resource allocation.
Our specialized skills in developing Proof of Concepts (PoCs) and Minimum Viable Products (MVPs) enable organizations to assess the potential impacts of AI tools in practical applications, ensuring that solutions are optimized for production planning needs.
Our expertise in generative AI extends to streamlining routine tasks such as report generation, data management ,and prototype creation, automating these processes to enhance efficiency in production planning and allowing professionals to focus on more strategic responsibilities.
By systematically refining large language models tailored to manufacturing terminology and client interactions, LeewayHertz optimizes the precision and applicability of AI-driven production strategies and decision-making processes in production planning contexts.
Moreover, we ensure seamless integration of these AI systems with current technological infrastructures, boosting operational efficiency and facilitating informed decision-making within production planning processes.
Our AI solutions development expertise
In production planning, AI solutions are designed to enhance decision-making, automate routine tasks, and personalize client services. These solutions integrate advanced data aggregation technologies to compile and analyze production information from diverse sources. This comprehensive data foundation supports predictive analytics capabilities, allowing for forecasting market trends that inform strategic decisions. Additionally, machine learning algorithms are employed to tailor processes and strategies to specific needs, ensuring efficient operations and strategic planning across areas like production scheduling, demand forecasting, inventory management etc
Overall. AI solutions in production planning aim to optimize outcomes, improve operational efficiency, and enhance the client experience.
AI agent/copilot development for production planning
LeewayHertz develops custom AI agents and copilots that streamline various production planning operations, allowing companies to conserve time and resources while expediting decision-making processes. Here’s how they help:
Production planning and scheduling
- Leverage historical data and real-time market trends to forecast product demand accurately, optimizing inventory levels and reducing overproduction or stockouts.
- Automate the creation of production schedules that balance resource availability, production capacities, and delivery deadlines to maximize efficiency and minimize downtime.
- Analyze production requirements to allocate resources effectively, ensuring optimal utilization of machinery, labor, and materials.
Prototype designs
- Use AI agents to analyze and refine prototype designs based on performance data and simulation results, improving product quality and reducing time-to-market.
- Leverage AI agents to create and test virtual prototypes, allowing for faster iterations and cost-effective design adjustments without physical prototypes.
Process automation and improvements
- Utilize AI agents to monitor and inspect production quality in real-time, detecting defects or anomalies and enhancing automated quality assurance processes.
- Predict and address maintenance needs before equipment failures occur by analyzing usage patterns and wear-and-tear data, minimizing downtime and maintenance costs.
Supply chain integration
- Analyzing historical data and current performance metrics can automate supplier selection and performance evaluation, ensuring reliable and cost-effective sourcing.
- Optimize transportation and logistics by using AI agents to analyze routes, manage shipments, and reduce costs while improving delivery times.
Process efficiency
- Streamline administrative tasks such as order processing, inventory management, and procurement to reduce manual effort and operational overhead.
- Analyze production data to identify bottlenecks, inefficiencies, and opportunities for process improvements, leading to more effective and efficient production operations.
Customer and market insights
- Use AI agents to analyze market trends and customer preferences, informing production planning decisions to align with current and future market demands.
- Offer customized production options based on individual customer preferences and specifications, enhancing customer satisfaction and competitive edge.
Integrating advanced AI solutions into production planning boosts operational efficiency and elevates customer service quality and strategic decision-making. These AI tools empower firms to gain a competitive edge in navigating complex production landscapes, offering innovative, efficient, and dependable strategies and tools driven by AI technology.
Future trends in AI-enhanced production planning and scheduling
As artificial intelligence continues to advance, its impact on production planning is becoming increasingly profound. Future trends indicate a transformative shift towards more accurate forecasting, autonomous decision-making, and enhanced sustainability, driven by innovations in AI and its integration with emerging technologies.
- AI-powered demand sensing: AI will transform demand forecasting by continuously analyzing real-time data from diverse sources such as global events and social media trends. This will enable manufacturers to generate more accurate and timely forecasts, allowing for swift adaptation to dynamic market conditions.
- Integration of AI and IoT for real-time data insights: The seamless integration of AI with IoT devices will provide manufacturers with a comprehensive and real-time view of production processes. This convergence will enhance decision-making accuracy, enable predictive maintenance, and optimize production scheduling based on current data.
- The exponential growth of predictive analytics: Predictive analytics will advance significantly, driven by improvements in machine learning algorithms and increased access to big data. AI will predict demand and foresee potential machine failures, supply chain disruptions, and other bottlenecks, thereby minimizing risks and boosting production efficiency.
- AI-driven autonomous decision-making: AI systems will evolve to make complex decisions autonomously through reinforcement learning and advanced cognitive computing. This shift will enable real-time decision execution, streamlining production planning and reducing the need for constant human intervention.
- Enhanced human-machine collaboration: Future AI systems will be developed to improve the synergy between humans and machines. These systems will become more intuitive and user-friendly, enabling non-technical users to interact effectively with AI technologies and leverage them as tools to augment human decision-making.
- AI for sustainable production practices: AI will play a crucial role in optimizing production for sustainability. Machine learning algorithms will assess environmental impacts and recommend changes to reduce carbon footprints, implement energy-efficient scheduling, and adopt waste reduction strategies, thus advancing sustainable manufacturing practices.
- AI-enhanced cybersecurity measures: AI will increasingly fortify cybersecurity in manufacturing by continuously analyzing data for security threats, detecting anomalies, and responding to potential cyber-attacks in real-time. This proactive approach will protect production planning systems from unauthorized access and malicious activities.
Endnote
In the world of manufacturing, where every second counts and adaptability is key, the role of AI in production planning and scheduling has proven transformative. The once-static schedules and rigid production processes are being replaced by intelligent systems that analyze data, detect defects in real time, optimize resource allocation, and ensure on-time deliveries. The questions we posed at the beginning of this journey are no longer hypothetical; they’re the driving force behind innovation and transformation.
AI’s ability to analyze historical data with uncanny accuracy empowers production planners to anticipate and prepare for future production needs, minimizing waste and maximizing efficiency. Computer vision ensures product quality and safety through real-time defect detection. Natural Language Processing streamlines communication and decision-making, and predictive analytics, coupled with IoT integration, minimize downtime and optimize production schedules.
As we look to the future, the possibilities are boundless. AI-enhanced production planning and scheduling isn’t just a trend; it’s a new standard that will continue to shape the industry. The factories of tomorrow will be smarter, more responsive, and more efficient thanks to AI. With AI leading the way, we can expect even more innovations, greater cost-efficiency, and an industry that stays at the forefront of global manufacturing trends. So, let’s embrace the future, where the fusion of human intelligence and AI-driven insights propels us toward manufacturing excellence. The age of smart manufacturing has arrived, and it’s here to stay.
Unlock the potential of AI in production planning and scheduling to optimize your manufacturing processes and enhance efficiency. Discover the future of smart manufacturing now and reach out to Leewayhertz’s AI experts for guidance.
Start a conversation by filling the form
All information will be kept confidential.
FAQs
How does AI improve production planning efficiency?
AI enhances production planning efficiency by analyzing large datasets, identifying patterns, and making accurate predictions. It can optimize production schedules, minimize downtime, reduce waste, and improve resource utilization, ultimately leading to cost savings and increased productivity.
What AI technologies are commonly used in production planning?
AI technologies commonly used in production planning include machine learning algorithms for demand forecasting, predictive analytics for identifying bottlenecks and optimizing workflows, natural language processing (NLP) for analyzing unstructured data, and computer vision for quality control and defect detection.
How does AI address challenges in production planning?
AI addresses challenges in production planning by automating repetitive tasks, providing real-time insights, improving demand forecast accuracy, optimizing inventory levels, and enabling agile and responsive production processes to adapt to changing market conditions.
How can LeewayHertz assist in implementing AI solutions for production planning?
LeewayHertz offers expertise in developing custom AI solutions tailored to specific production planning needs. Our team collaborates closely with clients to comprehend their requirements. We then design AI solutions that optimize production schedules, improve resource allocation, and enhance overall efficiency.
How does AI address challenges in production planning stages?
AI addresses challenges in production planning stages by offering advanced analytics, machine learning capabilities, and optimization algorithms. It enhances the efficiency and effectiveness of production planning processes by providing data-driven insights and continuous process optimization.
How does LeewayHertz ensure data privacy in AI-driven production planning solutions?
At LeewayHertz, data privacy is a top priority in all our projects, including AI-driven production planning solutions. We employ stringent security measures such as encryption and compliance with data protection regulations to safeguard sensitive production data. Additionally, we adhere to industry best practices and standards to ensure confidentiality and integrity throughout the data lifecycle.
What makes LeewayHertz a reliable partner for AI in production planning?
LeewayHertz offers vast expertise in AI development and a demonstrated history of delivering successful projects in production planning. Our team consists of proficient AI engineers, data scientists, and domain experts dedicated to crafting innovative solutions tailored to the specific needs of manufacturing enterprises.
How does LeewayHertz ensure continuous improvement and support for AI-based production planning systems?
Yes, LeewayHertz offers comprehensive support and maintenance services to ensure the smooth operation of AI-based production planning systems. We provide regular updates, performance monitoring, troubleshooting, and optimization to maximize the effectiveness and efficiency of the deployed solutions.
How do I start a project with LeewayHertz for AI in production planning?
To begin a project with LeewayHertz, simply reach out to us via our website or email us at sales@leewayhertz.com. After understanding your requirements, we’ll conduct an initial consultation to assess your needs, discuss potential solutions, and outline the project scope, timeline, and budget. Our expert team will then develop an AI solution tailored to your production planning challenges and objectives. Throughout the project, we’ll provide regular updates and support to ensure successful implementation.